What is “gauge” meaning for aluminuum sheet?
In the context of aluminum sheets, “gauge” refers to the thickness of the sheet. It’s a standardized measurement system used to indicate the thickness of an aluminum sheet metal.
There are two gauge systems used for aluminum sheets:
- American Wire Gauge (AWG): Ranges from 8 to 30, with the higher numbers indicating thinner sheets.
- Standard Wire Gauge (SWG): Ranges from 6 to 30, with the higher numbers indicating thicker sheets.
The most common aluminum sheet gauges range from 22-gauge to 10-gauge, with corresponding thicknesses ranging from approximately 0.0253 inches to 0.1019 inches. Different gauges are suitable for different applications, such as roofing, building facades, and automotive parts.
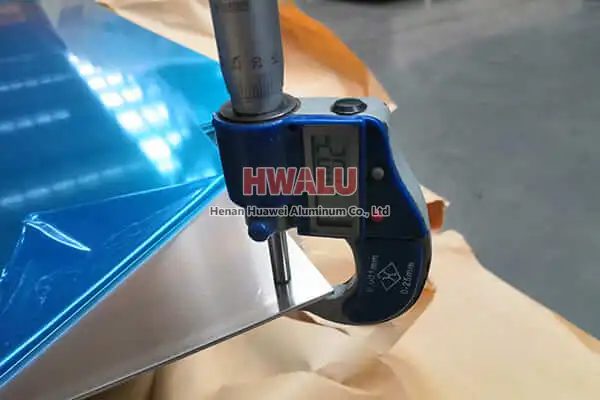
When selecting an aluminum sheet gauge, several factors must be considered to ensure that the chosen gauge will meet the requirements of the specific application. These factors include the strength of the sheet, the weight of the sheet, the cost of the sheet, and the corrosion resistance of the sheet.
Remember, the exact meaning depends on the context in which the term “gauge” is being used. For example, a 22-gauge aluminum sheet is often used for roofing and building facades, while a 16-gauge aluminum sheet is commonly used for automotive parts. It’s important to choose the right gauge for the intended application to ensure the strength and durability of the aluminum sheet.
What is 12 gauge aluminum sheets
12 gauge aluminum sheet refers to an aluminum sheet with a thickness of 0.0808 inches or 2.052 millimeters. This thickness is close to 2mm, making it a commonly used size in various applications.
In terms of its properties, 12 gauge aluminum sheet can be used in contact with food, has good weldability, and can be surface treated with protective anodizing. It also has very good cold formability, which includes bending, pressing, deep drawing, upsetting, and impact extrusion.
Advantages of using 12 gauge aluminum sheets
12 gauge aluminum sheets offer several advantages in various applications:
- Thickness and Robustness: 12 gauge aluminum sheets are 30% thicker and more robust compared to 14ga aluminum sheet. This makes them more durable and resistant to damage, which is beneficial in applications where the material may be subjected to significant stress or wear.
- Rust Warranty: 12 gauge aluminum sheets often come with a 20-year rust warranty. This is a testament to their durability and resistance to corrosion, which can extend the lifespan of products made from these sheets.
- Suitable for Heavy Snowfall Areas: If you are in an area that gets heavy snowfall, 12 gauge aluminum sheets are highly recommended. Their thickness and strength make them capable of withstanding the weight of heavy snow.
- Cost-Effective: Aluminum sheets are relatively inexpensive compared to other materials such as steel or plastic. This makes them a great choice for businesses looking to reduce their costs.
- Recyclable: Aluminum sheets are recyclable, which means they can be reused multiple times, further reducing costs and contributing to environmental sustainability.
- Versatility: Aluminum is recognized for being both lightweight and flexible. It can be cast, melted, formed, machined, and extruded, meaning that it can be manufactured into a variety of shapes and subsequently fabricated to suit a whole variety of uses.
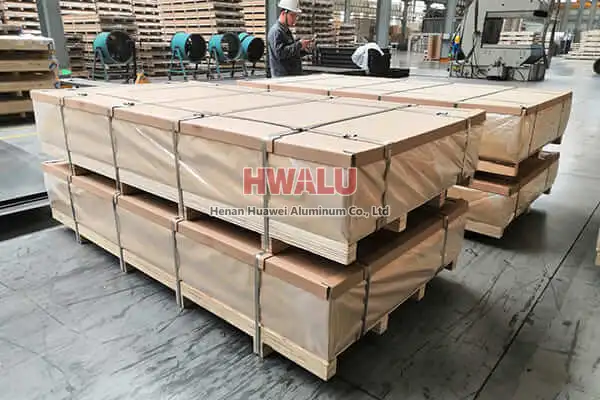
Properties and characteristics of 12 gauge aluminum sheets
12 gauge aluminum sheets have several properties and characteristics that make them suitable for a variety of applications:
- Thickness: 12 gauge aluminum sheet has a thickness of 0.0808 inches or 2.052 millimeters. This thickness is close to 2mm, making it a commonly used size in various applications.
- Weight: The weight per unit area of a 12 gauge aluminum sheet is approximately 1.14 lb/ft² or 5.567 kg/m². This weight and thickness are important factors to consider in applications where the strength and weight of the material can impact the performance and efficiency of the end product.
- Corrosion Resistance: Aluminum sheets, including 12 gauge sheets, have good corrosion resistance3. This means they can withstand exposure to harsh environments without deteriorating quickly.
- Lightweight: Aluminum is a lightweight material, which makes 12 gauge aluminum sheets easy to handle and install.
- Good Mechanical Properties: Aluminum sheets have good mechanical properties, including strength and durability.
- Dimensional Stability: Aluminum maintains its shape and size under varying temperatures, making 12 gauge aluminum sheets stable in various conditions.
These properties make 12 gauge aluminum sheets suitable for a wide range of applications, including construction, automotive parts, and industrial manufacturing.
Applications of 12 gauge aluminum sheets in different industries
- Construction: Used in roofing, siding, gutters, and decorative trim due to its lightweight nature, corrosion resistance, and ease of fabrication.
- Automotive: Used in body panels, truck trailers, and automotive trim due to its strength, lightweight, and ability to be easily formed.
- Aerospace: Used in aircraft structures, interior panels, and fuel tanks due to its high strength-to-weight ratio and corrosion resistance.
- Marine: Used in boat hulls, masts, and components due to its resistance to saltwater corrosion.
- Electronics: Used in casings, heat sinks, and components due to its conductivity, lightweight, and heat dissipation properties.
- Packaging: Used in foil packaging and containers due to its ability to protect against light, moisture, and bacteria.
- Industrial: Used in machinery enclosures, storage tanks, and platforms due to its durability and corrosion resistance.
- Transportation: Used in truck beds, rail cars, and shipping containers due to its strength, lightweight, and durability.
Different types and finishes of 12 gauge aluminum sheets
12 gauge aluminum sheets are available in various types and finishes to suit different applications and aesthetic preferences. Some common types and finishes include:
Mill Finish: This is the standard finish for aluminum sheets straight from the mill. It has a dull appearance and is not coated or treated, making it suitable for industrial applications.
Anodized Finish: Anodizing is an electrochemical process that thickens the natural oxide layer on the surface of aluminum. This finish provides increased corrosion resistance and can be colored for decorative purposes.
Painted Finish: Aluminum sheets can be painted with a variety of coatings to provide additional protection and aesthetic appeal. These coatings can be applied in different colors and finishes, such as matte, glossy, or textured.
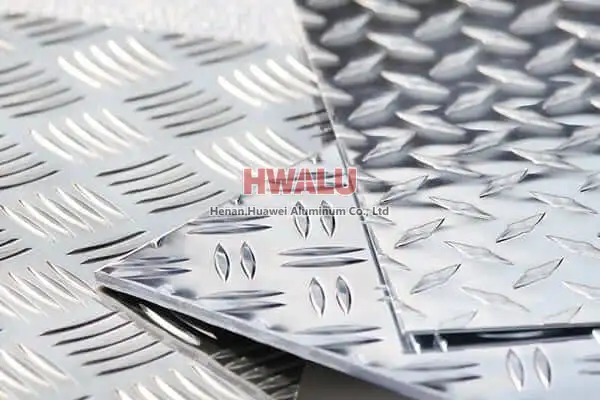
Embossed Finish: Aluminum sheets can be embossed with patterns or textures to improve grip, enhance aesthetics, or increase stiffness.
Brushed Finish: A brushed finish is achieved by mechanically polishing the surface of the aluminum sheet in one direction, creating a satin-like appearance. This finish is often used for decorative purposes.
Polished Finish: Aluminum sheets can be polished to a high gloss finish, which is suitable for decorative applications where a mirror-like appearance is desired.
Aluminum sheet manufacturers near me
Henan Huawei Aluminum Co., Ltd. is the leader of many aluminum manufactures and suppliers in China. We strictly control the quality and focus on customers. We hope to have in-depth cooperation with you and provide you with high quality aluminum material products custom OEM services. If you want to get the newest and best prices by per kg ( kilogram ) or per ton standard weight, please contact us.
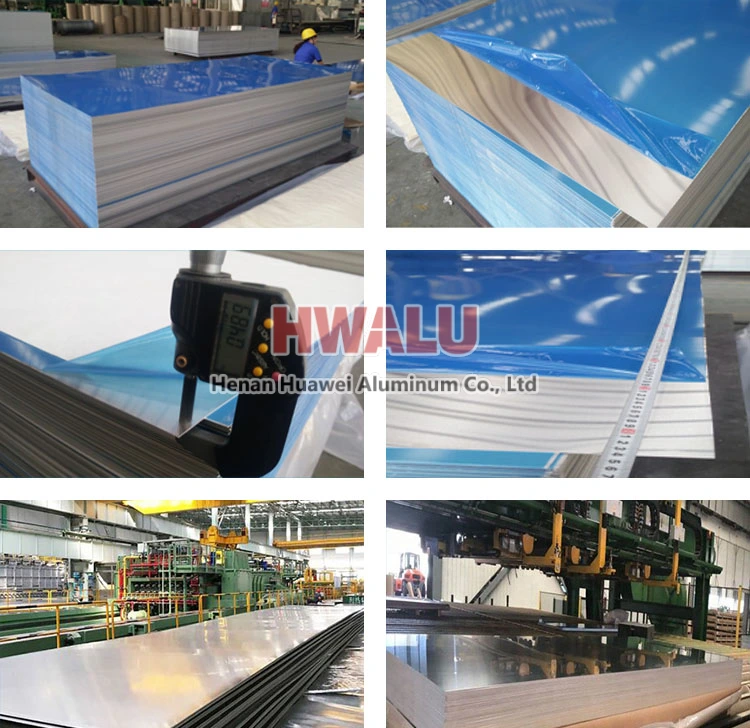
Aluminum sheet plate standard export packing
- The aluminum plate is paperclip or laminated to ensure that the surface of the aluminum plate is intact and free of scratches;
- Plastic film ( HDPE, PVC, PE or PET etc ) protection or hard kraft paper wrapping is used to prevent moisture and rain to ensure that the aluminum plate is clean and free of dirt during transportation (each package has a moisture-proof desiccant to ensure the quality of our products in East China and South China, where there is more rain);
- Installed with wooden brackets and reinforced with steel straps to avoid collision during transportation and to ensure the geometry of the aluminum plate remains unchanged;
- For export products, we use wooden boxes and pallets with fumigation mark for packaging;
- We can also pack according to other packaging requirements of customers;
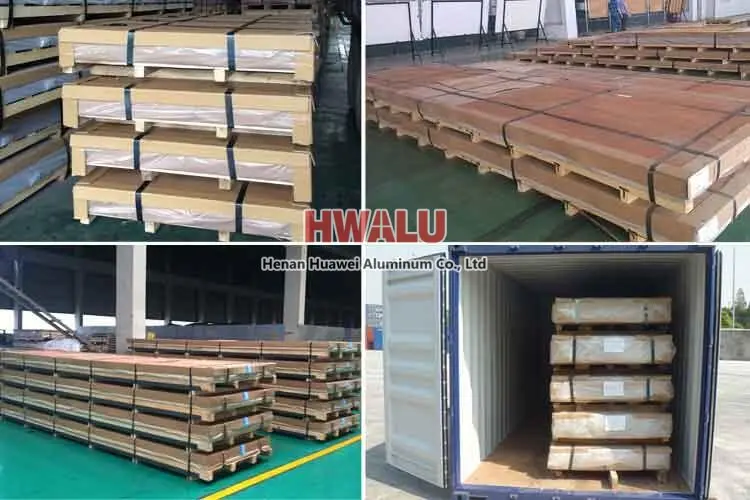